L姐有话说:
丰田汽车致力于开发简单、细长、小巧的生产技术。我们有幸对这一“秘中之秘”的最新生产设备进行了采访。虽然制造的都是一般汽车的零部件,但其制造方法是划时代的。可以说,其他汽车制造商不敢尝试,也无法复制这套制造方法。这款生产设备极具灵活性,那它具体是在制造什么,又是怎样制造的呢?
答案就在下文。(经丰田汽车要求,已对部分图像进行加工)
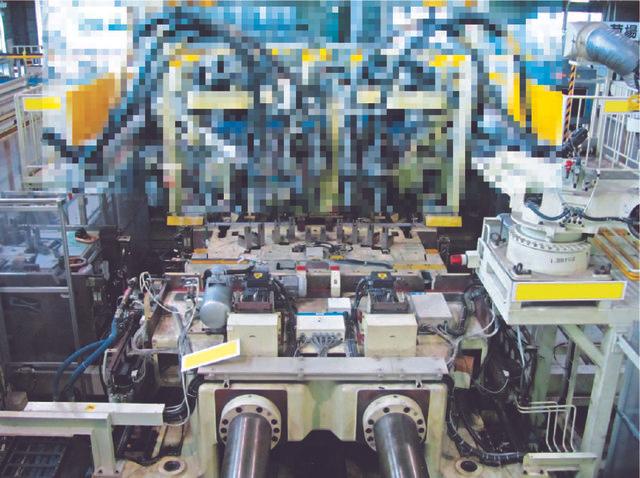
丰田汽车最新生产设备
多种保险杠的混合生产
运行该生产设备的是丰田汽车的成品工场——高冈工场。在第二组装生产线的成型工序中,该生产设备通过注塑成型将多种保险杠混合在一起进行生产,即“保险杠的混合生产”。
例如,成型混合动力车“Priusα”和“Wish”的前后保险杠的基本步骤是:
(1)成型“Priusα”的前保险杠后,对同一车种的后保险杠进行成型;
(2)成型“Wish”的前保险杠后,对同一车种的后保险杠进行成型(图1)。
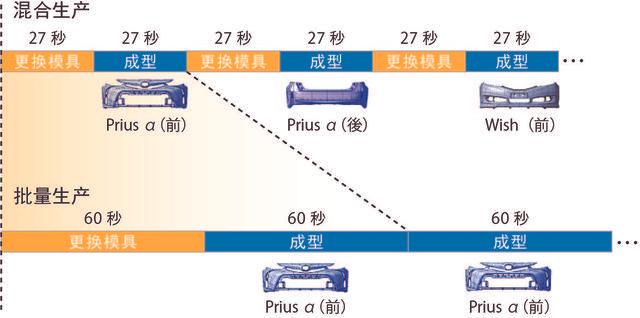
图1:保险杠的成型周期
上面为保险杠的新生产设备,成型和模具更换仅为27秒的混合生产。下面为以往的保险杠生产设备,成型和模具更换都需要60秒,是同时生产几十个同样的保险杠。
现阶段,该生产设备与4个车种、年产10万台的混合生产线配合,具备成型4个车种前后保险杠(总计8种保险杠)的实力。
通常,树脂的注塑成型除了要考虑成型时间以外,还要考虑模具更换时间,所以批量生产是最为常见的生产方法。此前,丰田汽车采用的也是这种方法。
多点注入树脂
具备6个小型柱塞(小型注塑机)的注塑机“TIM(TOYOTA INJECTION MACHINE)”是此次导入的新生产设备的核心成分[图2(a)]。它能独立控制各个小型柱塞,从6个地方向模具注入树脂。这样一来,流道(从喷嘴到成型制品边缘的距离)变短,树脂更容易到达模具的各个角落,进而缩短成型时间。
此外,丰田还进一步缩短时间,在向模具注入树脂的同时进行“真空”处理——通过负压减少空气阻力,使树脂更容易注入。其中,树脂采用的是丰田材料技术部开发的聚丙烯(PP)系列树脂“TOYOTA SUPER OLEFIN POLYMER”。该树脂兼顾高流动性和高刚性,能够顺利完成薄壁成型。
就这样,丰田成功将成型时间由原来的60秒缩短到了27秒。
将取出成型制品的夹具通用化
多点注入的方法在缩短模具更换时间上也贡献了力量,因为采用多点注入方法的TIM并不需要柱塞承受太大的压力——以往都是用一台大型注塑机将树脂注入模具[图2(b)],由于流道又长又复杂,为使树脂能从多个分叉流道流入模具的各个角落,需要柱塞加大压力。

图2:注塑机的概念图和成型的解析结果(压力)
(a)丰田汽车开发的注塑机。其具备6个小型柱塞(平面图中只显示5个),能够分散向模具注入树脂,缩短成型时间。模具的注塑点和边缘的压力差减小,锁模力变小,模具的强度降低。(b)以往的注塑机,市面上卖的机型。大型注塑机从单一处向模具注入树脂,模具的注塑点与边缘的压力差较大,锁模力变大,对模具的强度要求较高。
与此相对,使用TIM后,由于流道变短,注塑点和边缘的压力差会变小(锁模力变小),对模具强度的要求也会下降,这使得模具能够小型化、轻量化,容易移动和更换。
逐一制造模具时,通过自动交换装置,成型一次就要更换一次模具。模具与自动交换装置分别位于注塑机的左右两边(图3),成型过程中就要准备好下一个模具,以便将成型结束的模具取下、排出后,迅速投入下一个模具。

图3:新保险杠生产设备的构造
俯视布局图。中央是注塑机,左右两边配置有自动模具交换装置。成型过程中需要准备好下一个模具,以便成型后自动进行模具排出和新模具投入的更换工作。
与模具交换同样需要缩短时间的是取出成型制品的工序。以往将单个不同种类的成型制品取出时,需要更换机器人手臂前端的夹具,花费一定的时间。为此,丰田汽车开发了一套通用夹具。
该夹具具备18个吸附盘,可通过负压吸附成型制品,即便有些吸盘闲置,其他吸盘也能把持住模具,以对应不同种类的成型制品。
通过以上方法,模具的交换时间和成型时间也由原来的60秒缩短至27秒,即:新生产设备是27秒更换模具和27秒成型,54秒就可以成型一个保险杠,单件生产时间低于60秒。
此外,经由混合生产,保险杠的中间库存也没有了,因为成型工序与随后的涂装工序能够直接连续。这也使得工厂面积缩小了3成。
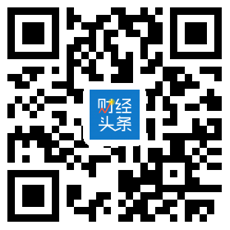
4000520066 欢迎批评指正
All Rights Reserved 新浪公司 版权所有