作为一个操作数控机床进行生产和加工零部件的企业,他的每个员工多必须知道下面我所说的关于数控机械加工的事项,它可以让我们更清楚和了解我们自己的机床,也可以少走很多弯路
1.数控机械加工一般操作步骤
(l)书写或编程加工前应首先编制工件的加工程序,如果工件的加工程序较长且比较复杂时,最好不要在机床上编程,而采用编程机或电脑编程,这样可以避免占用机时,对于短程序也应写在程序单上。最好等编辑完成之后先试用一下,以免正式加工造成不必要的浪费。
(2)开机一般是先开机床再开系统,有的设计二者是互锁的,机床不通电就不能在CRT上显示信息。另外来说一上来开系统在开机,很容易出现一个问题就是之前编写好的程序一开机运行,这样可能会有潜在的危险。就好比车子挂好了档位之后在点火,这样很危险。
(3)回参考点对于增量控制系统(使用增量式位置检测元件)的机床,必须首先执行这一步,以建立机床各坐标的移动基准。
(4)调加工程序根据程序的存储介质(纸带或磁带、磁盘),可以用纸带阅读机、盒式磁带机、编程机或串口通信输入,若是简单程序可直接采用键盘在CNC控制面板上输人,若程序非常简单且只加工一件,程序没有保存的必要。可采用MDI方式逐段输人、逐段加工。另外,程序中用到的工件原点、刀具参数、偏置量、各种补偿量在加工前也必须输人。当然了,我们一般的人不肯能只加工一个工件。
(5)程序的编辑输人的程序若需要修改,则要进行编辑操作。这中间一定要把机器暂定,此时,将方式选择开关置于编辑位置,利用编辑键进行增加、删除、更改。关于编辑方法可见相应的说明书。
(6)机床锁住,运行程序此步骤是对程序进行检查,若有错误,则需重新进行编辑。
(7)上工件、找正对刀采用手动增量移动,连续移动或采用手摇轮移动机床。将起刀点对到程序的起始处,并对好刀具的基准。
(8)启动坐标进给进行连续加工一般是采用存储器中程序加工。这种方式比采用纸带上程序加工故障率低。加工中的进给速度可采用进给倍率开关调节。加工中可以按进给保持按钮,暂停进给运动,观察加工情况或进行手工测量。再按下循环启动按钮,即可恢复加工。为确保程序正确无误,加工前应再复查一遍。在铣削加工时,对于平面曲线工件,可采用铅笔代替刀具在纸上面工件轮廓,这样比较直观。若系统具有刀具轨迹模拟功能则可用其检查程序的正确性。
(9)操作显示利用CRT的各个画面显示工作台或刀具的位置、程序和机床的状态,以使操作工人监视加工情况。
(10)程序输出加工结束后,若程序有保存必要,可以留在CNC的内存中,若程序太长,可以把内存中的程序输出给外部设备(例如穿孔机),在穿孔纸带(或磁带、磁盘等)上加以保存。
(11)关机一般应先关机床再关系统。
2.数控机械加工操作过程中的注意事项
(l)每次开机前要检查一下铣床后面润滑油泵中的润滑油是否充裕,空气压缩机是否打开,切削液所用的机械油是否足够等。
(2)开机时,首先打开总电源,然后按下CNC电源中的开启按钮,把急停按钮顺时针旋转,等铣床检测完所有功能后(下操作面板上的一排红色指示灯熄掉),按下机床按钮,使铣床复位,处于待命状态。
(3)在手动操作时,必须时刻注意,在进行X、Y方向移动前,必须使Z轴处于抬刀位置。移动过程中,不能只看CRT屏幕中坐标位置的变化,而要观察刀具的移动,等刀具移动到位后,再看CRT屏幕进行微调。
(4)在编程过程中,对于初学者来说,尽量少用G00指令,特别在X, Y,Z三轴联动中,更应注意。在走空刀时,应把Z轴的移动与X、Y轴的移动分开进行,即多抬刀、少斜插。有时由于斜插时,刀具会碰到工件而发生刀具的破坏。
(5)在使用电脑进行串口通信时,要做到:先开铣床、后开电脑;先关电脑、后关铣床。 避免铣床在开关的过程中,由于电流的瞬间变化而冲击电脑。
(6)在利用DNC(电脑与铣床之间相互进行程序的输送)功能时,要注意铣床的内存容量,一般从电脑向铣床传输的程序总字节数应小于23kB。如果程序比较长,则必须采用由电脑边传输边加工的方法,但程序段号,不得超过N9999。如果程序段超过1万个,可以借助MASTERCAM中的程序编辑功能,把程序段号取消。
(7)铣床出现报警时,要根据报警号查找原因,及时解除报警,不可关机了事,否则开机后仍处于报警状态。 采用寻边器对刀,其详细步骤如下:
( 1 ) X 、 Y 向对刀
①将工件通过夹具装在机床工作台上,装夹时,精密零件的四个侧面都应留出寻边器的测量位置。
②快速移动工作台和主轴,让寻边器测头靠近工件的左侧;
③改用微调操作,让测头慢慢接触到工件左侧,直到寻边器发光,记下此时机床坐标系中的 X 坐标值, 如 -310.300 ;
④抬起寻边器至工件上表面之上,快速移动工作台和主轴,让测头靠近工件右侧;
⑤改用微调操作,让测头慢慢接触到工件左侧,直到寻边器发光,记下此时机械坐标系中的 X 坐标值,如 -200.300 ;
⑥若测头直径为 10mm ,则工件长度为 -200.300-(-310.300)-10=100 ,据此可得工件坐标系原点 W在机床坐标系中的 X 坐标值为 -310.300+100/2+5= -255.300 ;
⑦同理可测得工件坐标系原点 W 在机械坐标系中的 Y 坐标值。
( 2 ) Z 向对刀
①卸下寻边器,将加工所用刀具装上主轴;
②将 Z 轴设定器(或固定高度的对刀块,以下同)放置在工件上平面上;
③快速移动主轴,让刀具端面靠近 Z 轴设定器上表面;
④改用微调操作,让刀具端面慢慢接触到 Z 轴设定器上表面,直到其指针指示到零位;
⑤记下此时机床坐标系中的 Z 值,如 -250.800 ;
⑥若 Z 轴设定器的高度为 50mm ,则工件坐标系原点 W 在机械坐标系中的 Z 坐标值为 -250.800-50-(30-20)=-310.800 。
( 3 )将测得的 X 、 Y 、 Z 值输入到机床工件坐标系存储地址中( 一般使用 G54-G59 代码存储对刀参数 )。
3 、注意事项 在对刀操作过程中需注意以下问题:
( 1 )根据加工要求采用正确的对刀工具,控制对刀误差;
( 2 )在对刀过程中,可通过改变微调进给量来提高对刀精度;
( 3 )对刀时需小心谨慎操作,尤其要注意移动方向,避免发生碰撞危险;
( 4 )对刀数据一定要存入与程序对应的存储地址,防止因调用错误而产生严重后果。
二、刀具补偿值的输入和修改 根据刀具的实际尺寸和位置,将刀具半径补偿值和刀具长度补偿值输入到与程序对应的存储位置。 需注意的是,补偿的数据正确性、符号正确性及数据所在地址正确性都将威胁到加工,从而导致撞车危险或加工报废
本文是由志宇精密机械加工原创 转载请注明http://www.jszycnc.com/ch/NewsView.asp?ID=392&SortID=10 详情您还可关注更多的新闻资讯,或者关注我们的微信公众号,了解更多关于精密零件加工的相关知识,具体定制详情可来电:13951155002 公众号:志宇精密零件加工
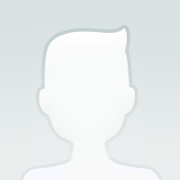
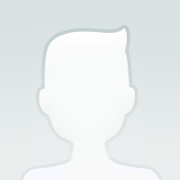
财经自媒体联盟
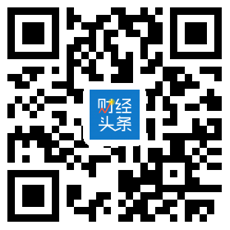
4000520066 欢迎批评指正
All Rights Reserved 新浪公司 版权所有