等静压模具的设计与制造,特别是在非标与异形产品的应用中,是一项高度定制化和技术密集型的工程。这类模具的设计不仅要满足特定产品的几何形状和尺寸要求,还要确保在高压环境下材料的均匀致密化,从而生产出高精度、高性能的零部件。以下是对非标、异形等静压模具设计与制造关键点的深入探讨。
1. 精准需求分析
首先,设计前需与客户进行深入沟通,明确产品用途、材料特性、性能要求及预期产量等,这直接关系到模具的材料选择、结构设计及后续生产工艺的制定。非标和异形产品的独特性要求设计团队对产品应用有深刻理解,以便做出最适宜的设计决策。
2. 独特的模具结构设计
非标与异形模具设计的最大挑战在于如何在保证产品几何复杂度的同时,实现压力的均匀传递。设计师需运用三维建模软件(如SolidWorks、UG NX等)进行精准设计,考虑模具的分瓣结构、滑块、抽芯等复杂运动机构,确保模具在闭合状态下内部空间与产品形状完全匹配,同时预留足够的排气路径,防止成型过程中的气泡生成。
3. 材料与表面处理
针对非标、异形产品的特殊性,模具材料的选择尤为关键。常用材料包括高强度合金钢、硬质合金等,需兼顾耐压、耐磨、耐腐蚀等特性。此外,对模具表面进行硬化处理(如渗氮、PVD涂层)或纹理处理(如喷砂),可以有效提升模具的使用寿命和产品的脱模性能。
4. 流体力学与应力分析
通过计算机辅助工程(CAE)软件,如ANSYS或ABAQUS,进行流体力学模拟,评估液体介质在模具内部的流动情况和压力分布,确保压力均匀传递。同时,进行模具应力分析,预测模具在极端工作条件下的变形情况,为模具的强度和刚性设计提供依据,防止因高压导致的模具损坏。
5. 尺寸补偿与公差控制
考虑到等静压过程中材料的压缩率,设计师需预先计算并实施尺寸补偿,确保最终产品尺寸符合设计要求。此外,严格的公差控制对于保证异形产品各部分尺寸协调一致至关重要,这要求在模具制造和装配过程中实施高精度的测量与调整。
6. 密封技术与测试
非标和异形模具的密封是设计中的难点之一。采用高质量的密封圈和特殊的密封结构设计,如O型圈、V型圈或是定制密封组件,确保在高压环境下的密封可靠性。完成模具制造后,进行密封性能测试,如水压试验,验证模具在实际工作状态下的密封效果。
7. 可制造性与维护性考虑
设计时还应充分考虑模具的可制造性,简化复杂结构,减少加工难度与成本。同时,设计易于拆卸、更换易损件的结构,便于模具的日常维护与长期使用。
8. 客户反馈与迭代优化
初次试产后,收集客户反馈,对产品性能和模具设计进行评估,必要时进行设计调整与优化,直至满足最终的产品性能和生产效率要求。
总之,非标与异形等静压模具的设计与制造是一项涉及多学科交叉的系统工程,需要综合考虑材料科学、机械工程、流体力学等多方面因素,通过精细化设计与严格的质量控制,才能确保最终产品的质量与生产效率。随着技术的不断进步和市场需求的多样化,等静压模具的设计与制造将更加注重创新与个性化,以适应更广泛的工业应用需求。
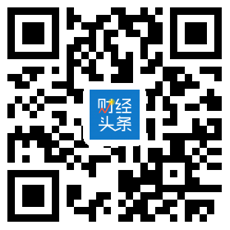
4000520066 欢迎批评指正
All Rights Reserved 新浪公司 版权所有