【精密制造新突破:等静压模具如何重塑陶瓷粉体成型技术】
在新材料领域,陶瓷粉体成型技术正经历着革命性变革。作为先进制造工艺的重要分支,等静压模具凭借其独特优势,正在为航空航天、电子元件、精密仪器等领域提供关键支撑。本文将深度解析这一技术的核心原理与应用价值。
一、等静压技术的核心优势传统干压成型存在密度不均、结构缺陷等问题,而等静压技术通过液体介质传递压力,实现 360° 均匀施压。这种各向同性的压力分布,使陶瓷坯体密度提升 30% 以上,有效消除内部微裂纹,显著提高材料强度与稳定性。数据显示,采用等静压工艺的陶瓷部件,抗折强度可达普通工艺的 1.5-2 倍。
二、工艺革新推动产业升级在电子陶瓷领域,5G 滤波器用陶瓷介质材料需满足高精度尺寸公差。等静压模具通过精准控制压力梯度,可实现 0.1mm 级超薄结构成型,突破传统工艺极限。某知名电子企业应用该技术后,产品良品率从 72% 提升至 91%,生产成本下降 40%。
三、技术发展的关键突破当前行业面临两大技术瓶颈:高温环境下的模具寿命与复杂结构的成型能力。海得实科技研发团队通过材料改性与结构优化,开发出耐 1500℃超高温的复合材料模具,同时采用参数化设计软件,实现异形结构的精准成型。其创新工艺已成功应用于某航天项目的热障涂层预制件制造。
四、行业应用的多元化拓展
- 新能源领域:固态电池电解质隔膜的均匀性直接影响电池性能,等静压工艺可实现纳米级孔隙率调控。
- 医疗行业:牙科陶瓷修复体的精密咬合面成型,要求尺寸精度达 ±20μm,该技术完美满足临床需求。
- 环保设备:脱硝催化剂载体的三维贯通孔结构,通过等静压工艺可实现 100% 连通率。
随着 "工业 4.0" 战略推进,智能模具系统正在成为新趋势。海得实科技研发的智能压力反馈系统,可实时监测成型过程,将工艺参数波动控制在 ±0.5% 以内,为工业 4.0 时代的柔性制造提供解决方案。
【结语】等静压模具技术的突破,不仅推动陶瓷材料性能提升,更催生出众多创新应用场景。在双碳目标指引下,这项绿色制造技术将持续赋能高端制造产业,为新材料革命注入核心动能。
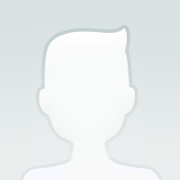
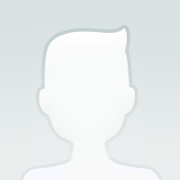
财经自媒体联盟
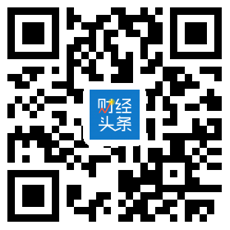
4000520066 欢迎批评指正
All Rights Reserved 新浪公司 版权所有