大型矿用挖掘机,又称电铲。其一铲斗的容量,相当于一节多火车车厢的容量,高度相当于8层楼高,体量比一个篮球场还大,总重量近2000吨,操作员坐在办公室里就能实现精准远程驾驶
在车轮厂二线,记者看到生产线的上方是工人所在的监测区,每道工序对应着一个集控室。在电子显示屏上,实时反映着产品温度等生产状况与产品生产进度,实现实时动态调整,“人”机娴熟配合,在流水线上各司其职
这些“智”造,源自工程师们脑子里的71000卷设计图纸。铺开这些设计图纸,长度可达400公里
文 |《瞭望》新闻周刊记者 王怡静
体量比一个篮球场还大、还能实现远程操控的矿用挖掘机;52秒即可下线一片轨道交通用车轮;没有驾驶室、实现语音操作的纯电动工程挖掘机……
走进太原重型机械集团有限公司(以下简称太重集团),从高速生产线到聪明的工业大块头,高端装备正在实现“智”造升级。
太重集团是重型设备智能化转型的生动缩影。在山西,通过技术突破推动智能化变革,不断提升生产效率与工作效率,优化生产流程和资源配置,正在传统行业中上演,越来越多“聪明的大块头”在市场涌现。
重型机械行业发展水平反映着制造业的发展水平。近年来,太重集团通过攻关关键核心技术,不断突破技术壁垒,将智能化改造融入到生产环节、运营方式、管理理念等方方面面,推动制造业高端化、智能化、绿色化发展。
研发出斗容最大的电铲
大型矿用挖掘机,又称电铲。其一铲斗的容量,相当于一节多火车车厢的容量,高度相当于8层楼高,体量比一个篮球场还大,总重量近2000吨,操作员坐在办公室里就能实现精准远程驾驶。
从“我不会造”到“仅我会造”,研发团队迎难而上、持续攻关,将“卡脖子”的技术转化为“杀手锏”。
1961年5月,我国在国外技术基础上,成功试制国内第一台4立方米矿用挖掘机WK-4,此后与外国开展合作生产挖掘机,但因无法掌握核心技术,大型矿用挖掘机长期被外国公司垄断。
憋足一股劲,太重集团下定决心,自主研发大型矿用挖掘机。大型矿用挖掘机的控制系统怎么选择?应该怎样变频?这么大体量的机器,电机容量如何控制?……第一台大型矿用挖掘机的研发,面临诸多挑战。
“对我们而言,这些是从0到1、从无到有的问题,不容许失败。因为一旦失败,不仅是上亿元的损失,更有可能打击我们实现自主创新的信心。”现年60岁的太重集团电气主任设计师刘晓星说。
电控系统是矿用挖掘机的核心技术,当时的直流控制系统是国外普遍采用且更成熟的系统,但研发团队大胆尝试,选择了更有发展前景的交流控制系统。“在运用层面,交流控制系统是一个相对空白的领域,但它能够实现平滑变速,效果好于直流控制系统。”刘晓星说。
经过无数次计算、数年摸索,2006年首台WK-20大型矿用挖掘机试制成功,结束了我国2000吨以上体量的露天矿用挖掘机长期被国外垄断的历史。在此基层上,经过研发团队6年努力,世界上斗容最大的大型矿用挖掘机在2012年成功下线。
“你可能感受不到这款电铲铲斗容量有多大,看个视频,就明白了。”刘晓星打开了一个现场作业的视频,视频里的工人还没有挖掘机最下方履带的一半高。
“设备的大型化并不是简单的等比例放大,其中涉及材料、力学、控制等诸多难题,从设计、研发到加工装配,上万个零件都必须精雕细琢。”太重集团技术中心矿山所电气专业技术负责人范喜斌介绍,10立方米体量的挖掘机重500吨,如果等比例放大,70立方米的挖掘机重量就将达到3500吨,而实际产品比这一数值轻了1500吨,以最低耗材达到最大载荷。
技术创新带动产品的更新换代,也催生着新的管理理念。“科技进步催动产业变革,行业的变革也要求我们必须用新思路新技术重塑流程和产品。”太重集团太原重工技术中心主任助理马立辉说。
此前传统重型机械企业缺少市场概念,曾面临无米下锅的窘境;走向市场后,又因重机产品普遍更重视社会效益,企业自身造血机能严重缺失,生存环境艰难。对此,太重推动“政治账、经济账、社会账改革”,以市场为导向,推动管理体制改革,加大科技开发与技术攻关投入。
2021年以来,太重连续4年召开科技质量大会,累计投入研发资金40亿元,年均增长25%。同时,通过“揭榜挂帅”和“赛马”机制,开展“卡脖子”技术攻关,攻克设计、工艺、智能化等关键核心技术。“2024年4月,太重拿出1854万元重奖科技成果创新人才,这对一线科技人员是很大的鼓舞。”马立辉说。
实现在办公室里开电铲
距离太原几百公里之外,在国家电投内蒙古霍林河露天煤业股份有限公司南露天煤矿上,身着白衬衣的电铲司机长贾文涛坐在远程操控室,操纵着5公里之外的大型矿用电铲,不一会儿工夫,矿车就被装满了。
这是5G远程操作大型矿用挖掘机的生动写照。通过远程操作,把人从电铲上、露天矿山的工作环境中解放出来,实现在办公室里开电铲。记者在太重集团展览中心体验了这一过程,坐在驾驶位上操纵手柄,眼前的屏幕上,挖掘机即刻开始运作,几乎感受不到时延,模拟震动感十分真实。
太重集团智能采矿装备技术全国重点实验室智能化所所长岳海峰介绍,太重的目标分为两个阶段,一是已经实现的远程操作,二是实现完全的无人操作,制造出拥有“智慧大脑”和“强健体魄”的电铲机器人,助力我国“智慧矿山”建设。
智能化矿用挖掘机“出生”的背后,曾困难重重。
首先,矿山地形复杂,远程控制需要极低时延,通信时延超过300毫秒,可能导致设备之间的碰撞,引发生产安全风险、造成重大经济损失。其次,相比实地操作,远程控制中驾驶员获得的信息量不足,可能影响操作的精准。此外,在机器执行操作阶段,并不能完全感知现场环境,容易出现卡顿、故障等风险。
岳海峰说,团队用了两年多时间,在机器感知—系统规划—执行操作全过程中,抠问题、找原因、做修改,写了上万个代码,最终研发出全链路140毫秒低时延传输、近180度裸眼3D沉浸式场景呈现、人工智能辅助一键精准控制、突发故障时安全性高的智控系统。
此外,矿用挖掘机加装更多智能化设备,促进重型设备的互联互通。借助数据分析和人工智能技术,设备能够不断学习和改进自身性能,适应不同的工作场景和需求。
岳海峰说,智能化应用大大降低工人的劳动强度,提高了生产效率。据测算,在相同工况下,这套系统平均每日作业时间能延长2个小时,整体作业效率较人工作业提高5%。
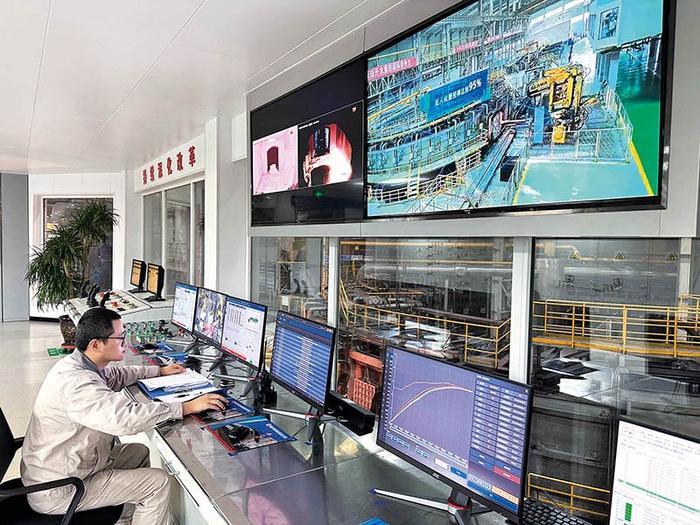
“灯塔工厂”打造竞争新优势
2024年10月8日,太原重工轨道交通设备有限公司获评全球轨道交通行业首座“灯塔工厂”。踏入轨道公司车轮厂二线,只觉热浪扑面而来,加热炉、智能机械手在有条不紊地进行作业。
一块特定尺寸的钢锭,经过1200多摄氏度高温煅烧,进入车轮全自动生产线。在生产线上,经过预成型、成型、轧制、压弯冲孔、打标、测量等工序,一片轨道交通用热态车轮就下线了。
智能化改造,不仅体现在生产环节的自动化、数字化,还体现在操作和管控环节的精准化、精细化上,助力企业不断提升生产效率和生产质量。
在车轮厂二线,记者看到生产线的上方是工人所在的监测区,每道工序对应着一个集控室。在电子显示屏上,实时反映着产品温度等生产状况与产品生产进度,实现实时动态调整,“人”机娴熟配合,在流水线上各司其职。
“以前在生产过程中,工人频繁地设定和调整加热炉的炉温,不仅耗时耗力,而且难以确保温度精准、加热均匀。”该公司设备能源室主管王沛说,现在有了智能燃烧控制系统的加持,加热炉能够自动精准地控制每一块钢坯的加热温度,降低缺陷率的同时,还提高了产品产量。
“‘灯塔工厂’通过智能化手段,把人从传统制造业流水线上解放出来,让智能化引领新质生产力的发展。”太原重工轨道交通设备有限公司副总经理芦树成说,这是质的变化,工人们成为管理机器人的人,带来了更高的效益。
经过不断研发,团队提高了车轮生产线的生产效率和产品质量,通过数次测试将车轮缺陷率降低了33%,将产量提高了33%,公司年产车轮70万片。
智能制造不仅是技术革新,更是生产模式的创新和变革,这些创新离不开人才和政策的支撑。
一块钢板用8.8分钟,跑过5公里长的生产线,变成了一台工程挖掘机。在太重智能高端工程挖掘机产业园区,1216台机器人、1216只挥舞的机械臂忙碌着,具备年产5万台挖掘机的生产能力。
这些“智”造,源自工程师们脑子里的71000卷设计图纸。铺开这些设计图纸,长度可达400公里,这长长的设计图纸,汇聚着70多年来的设计参数、设计标准等,如今已浓缩在太重各条智慧生产线中。
除了人才支撑,政策正在为智能转型注入动力。
据山西省工信厅消息,省级财政已拨付超过5亿元资金支持智能制造项目,拉动社会投资超过100亿元。山西省传统制造业重点领域基本实现数字化制造,重点产业智能转型取得明显进展。
近年来,太重集团建立“3+5+3”特色产品体系。“我们做强矿用挖掘机、工业起重机、冶金装备等传统产品,做优轨道交通部件、新能源装备、铸件锻件基础材料、高端液压件、高端数控机床等战略性新兴产品,做精智能工程起重机、工程起重机、新能源智能叉车等批量产品。”太重集团副总会计师、战略投资部部长邱英杰说。
随着智慧工厂投入使用,太重集团已具备年产300万吨装备的能力。如今,传统优势产品、战略性新兴产品和规模化批量产品,这三大板块齐发力,实现以“智”赋能,推动新质生产力发展。■
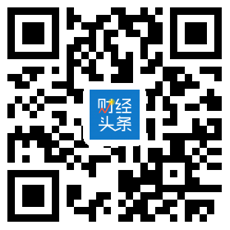
4000520066 欢迎批评指正
All Rights Reserved 新浪公司 版权所有