**引言**
在现代制造业中,**生产计划(MPS/MRP)** 是企业资源计划(ERP)系统的核心模块之一。它直接影响企业的生产效率、库存管理和供应链协同。那么,ERP系统是如何实现MPS(主生产计划)和MRP(物料需求计划)的?本文将深入解析其实现逻辑,并探讨实际应用中的关键点。
1. 什么是MPS和MRP?
**MPS(主生产计划,Master Production Schedule)**
MPS是**针对最终产品或关键部件的生产计划**,主要考虑市场需求、产能限制等因素,确保企业能按时交付客户订单。
**MRP(物料需求计划,Material Requirements Planning)**
MRP是基于MPS展开的**物料需求计算**,确定所有相关原材料、零部件的需求时间和数量,确保生产所需的物料供应。
**两者的关系**:
- **MPS** 决定“生产什么?何时生产?”
- **MRP** 回答“需要哪些物料?何时采购/生产?”
2. MPS/MRP的实现流程
**(1)基础数据准备**
ERP系统需要以下核心数据:
✅ **BOM(物料清单)**:定义产品的组成结构
✅ **库存数据**:当前可用库存、在途库存
✅ **工艺路线**:生产工序、工时、工作中心
✅ **供应商与采购提前期**:影响物料到货时间
✅ **销售订单与预测**:驱动生产需求
**(2)MPS主生产计划制定**
1. **需求管理**:合并销售订单与预测,确定优先级
2. **粗能力计划(RCCP)**:检查关键资源(如瓶颈设备)是否满足需求
3. **生成MPS**:结合库存、产能、交货期,制定生产计划
**(3)MRP物料需求计算**
MRP的核心计算逻辑:
1. **毛需求(Gross Requirement)** = MPS需求 × BOM用量
2. **净需求(Net Requirement)** = 毛需求 - 可用库存
3. **计划订单下达**:考虑采购/生产提前期,确保物料按时到位
**示例**:
假设要生产100台电脑(MPS需求),每台需要1块主板(BOM定义),当前库存有20块主板,则:
- **毛需求** = 100 × 1 = 100
- **净需求** = 100 - 20 = 80
- **计划采购订单** = 80块主板(需提前供应商交期下单)
---
3. 关键技术:如何优化MPS/MRP?
**(1)批量策略**
- **固定批量**:每次采购/生产固定数量(如100个)
- **按需定量**:完全匹配需求,减少库存
- **经济批量(EOQ)**:平衡采购成本与库存成本
**(2)替代料管理**
当主料缺货时,系统自动推荐替代物料,避免生产中断。
**(3)动态重排计划**
- **净改变法(Net Change)**:仅计算受影响的物料
- **再生法(Regeneration)**:全量重新计算(适用于大规模调整)
**(4)可视化与决策支持**
- **甘特图**:直观展示生产排程
- **负荷分析**:检查产能是否超负荷
- **What-if模拟**:预测计划调整的影响
4. 实际应用中的挑战
❌ **数据不准确** → BOM错误导致MRP计算偏差
❌ **计划僵化** → 无法快速响应插单、取消订单
❌ **系统性能问题** → 计算速度慢,影响决策效率
**解决方案**:
✔ **定期审核BOM和库存数据**
✔ **采用高级计划排程(APS)优化计算**
✔ **与MES(制造执行系统)集成**,实现实时反馈
5. 未来趋势:智能化MPS/MRP
- **AI预测需求**:更精准的销售预测
- **供应链协同**:与供应商实时共享需求计划
**结语**
MPS/MRP是ERP系统的“大脑”,直接影响企业的生产效率和成本控制。通过合理的计划逻辑、准确的数据和智能化技术,企业可以实现**更精准的生产排程、更低的库存、更高的交付率**。
本文来源:用友软件销售服务中心-新司南科技
原文地址:https://www.szyonsuite.com/article-detail/650.html
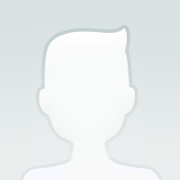
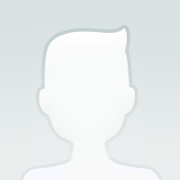
财经自媒体联盟
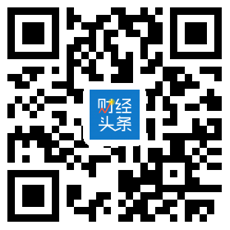
4000520066 欢迎批评指正
All Rights Reserved 新浪公司 版权所有