“质量就是生命,质量就是胜算!”在决胜冲刺的关键时期,航天科工全体干部职工坚决贯彻落实集团公司“四个确保”新时期质量工作方针,围绕“质量制胜”战略,不断强化“零缺陷”质量意识,促进科研生产质量管理能力提升,一切只为“保成功,保质量”!下面,请跟随航小科,走进一个个鲜活的“质量”故事。
激活质量数据,让数据主动发声
装备全寿命周期产生了海量元器件质量数据,如何才能让数据主动发声,充分发挥数据背后蕴含的价值,赋能装备质量管理具有重要的现实意义且需求紧迫。二院201所元器件可靠性技术研究中心质量大数据分析技术组正在推进的就是这样一份意义重大的开创性工作。
技术组深入分析元器件质保业务场景,识别、积累和分析各种关联数据资源,突破知识抽取、融合、推理等关键技术,发掘“隐藏”在大数据中的知识联系,打造百万级节点元器件质量管控知识图谱,以图形结构直观呈现知识之间关系,形成统一、完整的知识视图,通过运用机器学习算法和自然语言处理技术,精准理解并“捕获”用户意图,为用户答疑解惑,驱动知识管理模式由“人和文档为载体”向“数据为载体”转变,助力知识的高效共享和传承,促进跨班组、跨部门、跨专业的知识协同,提升组织的创新力和竞争力。
在艰辛攻关路上,他们取得了一系列的阶段性成果与关键技术突破:打通元器件清单、质量履历等数据链条,构建质量问题溯源模型,实现跨单机、跨型号、跨领域“举一反三”分秒溯源;突破元器件数据包络算法模型和预警技术,形成基于测试数据的批次元器件质量风险预警机制,识别关键质量参数,让数据主动“发声”,提前剥离可能造成事故的质量隐患。
技术组对每一行代码、每一张原型图都精雕细琢,不放过任何一个影响质量的细微之处,成功上线了数据标准化、清单风险评估、智能辅助审查等多套支撑工具,筑牢平台高效运转的技术堡垒,为大数据平台智能化源源不断地注入鲜活生命力。
做精小成果,展现大作为
近日,三院159厂QC成果“提高某箱体电子束焊接一次合格率”荣获2024年第49届国际质量管理小组大会金奖。成绩的取得,源自团队对于质量的不懈追求。
在一次任务中,159厂八分厂生产的120个复杂箱体,960条电子束焊缝中,焊接一次合格率为78.3%,这严重制约了总体进度,给生产带来巨大冲击。为此,159厂八分厂组建了“钣焊攻关”QC小组,将“提高某箱体电子束焊接一次合格率”作为攻关要务。大家根据各自擅长领域分头行动,查找缺陷原因。最终发现,环焊缝中未熔合和气孔占不合格项目的85.8%,是影响箱体电子束焊接一次不合格的主要症结。
小组成员从生产实际问题出发,从5M1E(造成产品质量波动的6个主要因素:人、机器、材料、方法、测量、环境)方面入手,针对未熔合和气孔症结进行原因分析,运用QC小组工具方法,最终确定了3项主要原因。通过优化焊接工装、优化焊接工艺流程、改进焊接工艺参数等措施,箱体电子束焊接一次合格率由之前的78.3%达到了活动后的92.9%,成功实现课题目标,有效提高箱体焊接一次合格率,提升了产品质量和工作效率。
“电子束焊接是自动化焊接技术之一,在159厂使用已经有23年,该课题的研究成果,进一步提高了产品的焊接合格率,减少了补焊次数,缩短了生产周期,同时也为同类产品电子束焊接提供了技术保障,提升了自动化焊接水平。”159厂八分厂梁主任说,“小组成员QC专业知识能力、创新能力、团结协作能力也得到了提高,增强了团队解决问题的信心。”
将质量管控提前到设计源头
深夜的调试间仍灯火通明,外协联合试验组成员正在紧张地开展试验。“试验先停下来”,四院十七所申博士突然说道。“怎么回事?数据采集是正常的”,大家满脸疑惑,纷纷凑过来一探究竟。原来,申博士利用早已准备好的试验数据实时判读工具,及时发现了试验异常的蛛丝马迹。
面对紧迫的任务节点,为紧抓宝贵的试验窗口期,及时识别产品技术故障,申博士利用所掌握的技能,创新开发出一款数据实时判读工具,动态进行数据监测,一举打破了在事后复盘时才能识别和分析问题的惯例。
一次试验中,该款工具的开发让一个偶发性故障被有效记录,保留了故障现场,为后续的原因分析提供了便利条件,同时也避免了盲目试验,提高了故障修复和试验工作的效率。
工作多年来,申博士始终坚信:产品研制过程是获得真知灼见的源头活水,设计师要真正融入产品研制一线,全面剖析产品的每一个细节,紧盯每一个试验过程,参透每一项试验数据,只有这样才能有效发现问题、解决问题。
在摸底试验的关键节点,申博士深入调试测试一线,敏锐发现了仪器上的一串可疑数据。经过询问得知,原来联试时设备曾出现过程序卡死的情况。虽然这个问题初步定位看似不会影响产品的正常功能,但在详细了解故障现象后,他秉持着“严慎细实”的工作态度开始重新排查、定位和分析问题。经过多日的联调联试,终于准确定位并解决了故障,成功避免了该单机偶发性故障在综合试验中可能导致的系统归零问题,真正做到了将质量管控提前到设计环节,从源头处寻找答案。
以“备预不虞”换取万无一失
晚上10点,漆黑的夜空星辰闪烁,指挥大厅庄重严肃。六院41所试验队指挥员的口令声铿锵有力。“5,4,3,2,1”,伴着隆隆的轰鸣声,一支喷射着尾焰的箭腾空而起,在夜空中划出一条漂亮的光带。“成功啦!”队员们击掌欢庆,每个人都难掩心中的激动与喜悦。
“严肃认真、周到细致、稳妥可靠、万无一失”,十六字方针标语不仅悬挂在会议室的墙上,也刻在每个试验队员的心里。
“安全第一”,试验队队长不仅把安全的事挂在嘴边,也付诸行动。技术安全责任书、现场应急处置方案、安全性分析报告等,都在他的要求下提高标准。“安全生产日检查、试验展开前安全检查……一项项安全措施都要做到百分之百全覆盖。”青年安全主管小弓回忆道。
在外场,质量管控是重中之重。试验队队员积极参与质量“双想”,提出的问题全部由专人负责闭环,确保没有遗留问题。“进场后产品各项检查测试、参试设备功能检查、技术状态变化控制……每一项质量控制环节都落到实处。”有30多年质量管理经验的质量主管吴姐介绍道。
关于试验队方方面面的计划调度,试验队队员通过边学习、边摸索、边总结,打造出41所特有的产品试验管理模式,确保了每项计划如期完成、每项质量控制落到实处、每项安全措施检查到位。
刮骨疗毒 洞察慧眼
在守好质量防线的道路上,“纠错”与“查漏”至关重要。九院红林公司装配车间技术员王欣蕾便是这方面的小能手。
“纠错”如刮骨疗毒,要有洞察“毒瘤”的慧眼。一次,王欣蕾主管的产品一组件焊线后,转到测试组进行电性能测试时,测试结果不合格,初步归因于焊接过程操作不当导致焊盘短路。但王欣蕾说:“这并非操作问题,同一批次中的电路板都出现了这样的情况,偶然操作不当不会导致同一批次都不合格。”她觉得应该从电路板找问题。后来,通过与印制板生产厂家沟通和实地调研,她发现,“病因”是两个焊盘的阻焊范围太小,导致焊接短路。
王欣蕾不仅找到了问题所在,还针对这一问题梳理了整改措施,建议调整传统装配工序,确保产品质量。装配工序调整后,工人发现在单板焊线时便能及时检查出短路问题,大大降低了产品返工率。
王欣蕾从细枝末节入手,一次又一次地将质量问题扼杀在“摇篮”中,为后续的线上生产建立了一座坚实的安全“堤坝”。
打造新时代质量管理体系
形势逼人、任务逼人、时间不等人,“2024年通过新时代装备建设质量管理体系三级评价为总体目标”在成立十院十部新体系建设专班时,便将“主攻目标”以文件形式加以明确。
新体系建设专班组建完毕,团队共有成员9名,来自战略规划、质量体系管理、预先研究、信息化、数字化等8个专业。专班职责任务同步明确,负责推进新体系三级建设的各项具体工作,瞄准新体系建设的难点、堵点等“要点山头”发起突击,朝着推动实现新体系“架构引领、流程主导、信息化支撑”的现代化管理目标和通过新时代装备建设质量管理体系三级评价的总体目标发起冲锋。
专班成立之初,因大部分专班成员在此前从未接触过新时代装备建设质量管理体系建设,对它的基本概念、建设标准与方法等都很陌生,对整个建设工作无从下手,以致工作启动非常困难、初期工作无法落地。“既然不懂,那就学懂弄通为止!”专班成员们通过积极咨询外部专家和自主学习专业知识,在极短的时间内,初步掌握理解新体系建设思路与方法,同时举一反三优化管理模式,将建设内容拆解细分为战略线、业务线、流程线等七条主线,设立专班秘书和指定各条线线长,由专班秘书制定双周滚动计划、月计划、季度计划,由各线长负责线上各类工作,以学赋能、管理清晰的他们迅速渡过了适应期,正式开启了新体系的建设之路。
经过持续半年的艰苦奋战,按照“架构引领、流程主导、信息化支撑”的理念,以“过程方法”原则为指导,成功交付了战略线、流程线等7条工作主线的建设成果。11月,经专家组评审,一致推荐十部注册新时代质量管理体系能力三级。专家组认为十部在推进目标转变、载体转变、方法转变、主体转变“四个转变”取得巨大进展,逐步实现提升内部管理、发挥流程价值链、强化精细化水平“三大目标”,实现了管理要求可落地,业务流程可执行,任务开展更高效的运营管理模式。

关于更多质量管理方法
请查看以下小贴士
二院283厂材料研发中心“慧眼”QC 小组凭借卓越表现,在这场被誉为“质量奥林匹克”的国际赛事中脱颖而出,斩获最高奖项金奖,在QC小组活动的推进过程中,283厂建立了一套完善的全过程质量管理体系,针对现场问题及内外部顾客及相关方需求,积极开展质量改进、质量创新。QC小组活动实现生产班组全覆盖,并向管理、职能领域延伸,营造出良好的质量氛围,助力质量管理水平不断提升。
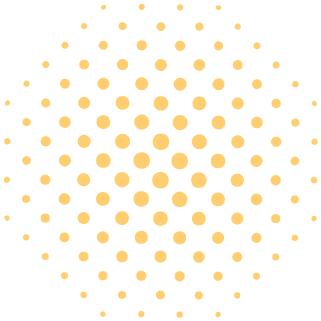
三院239厂作为总装厂,承担着航天产品的总装工作。操作过程需要充分运用多媒体记录,进行拍摄留存。总装检验组作为落实此项工作的主体班组,不仅需要反复琢磨拍摄技巧,把每一个插针都拍清楚,很多时候还需要拍摄侧面甚至背面的信息。为此,他们自己发明了“牙医拍摄法”,巧妙利用了牙医看病用的小镜子反光来拍摄连接器。而他们的“作品”也经受住了多次考验,为产品的复查发挥了重要作用。
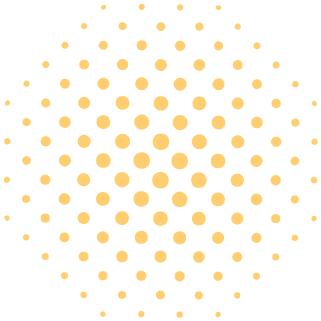
电动智能产线的投入使用,对产品加工质量管控提出了新要求。四院南京晨光公司十九分厂电装班组的韦组长是一名退伍军人,他积极学习先进质量管理方法,结合班组质量管理制度、模式、方法,提炼总结出“五步走”管理方法,即第一步看(工艺卡片)、第二步戴(静电防护)、第三步对(配套关系)、第四步动(产品装配)、第五步检(自检互查)。看似简单的“五步走”方法,通过各项质量改进措施,不断提高生产效率、降低不良品率。
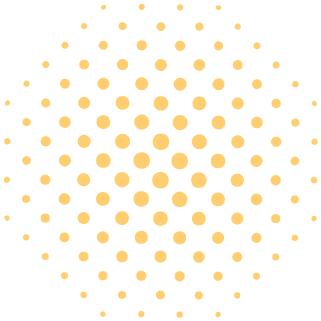
九院万山公司质量检验战线上负责喷涂相关检验工作的资深“老兵”陈克认为,“规范的操作是保证产品质量的基础。”在每一次检验时,他会严格对照油漆干燥时间表,根据时间、温度及湿度等关键因素,对每一个零部件进行细致入微的检测。他说:“如果产品表面油漆未干便转至下道工序,其表面油漆附着力差,容易影响产品质量。”所以,“油漆不干,绝不盖章!”便成了他的口头禅。
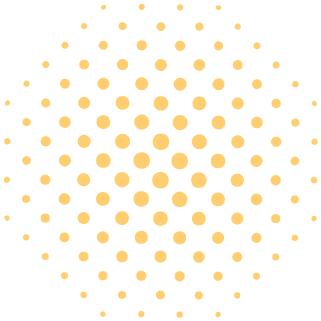
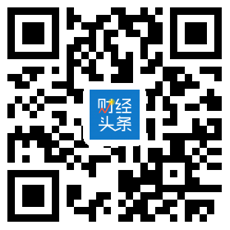
4000520066 欢迎批评指正
All Rights Reserved 新浪公司 版权所有