随着数字技术的快速发展,尤其是人工智能技术的突飞猛进,市场上已经涌现出众多预测性维护产品与解决方案提供商。然而,预测性维护落地比预想中困难。有数据统计,许多预测性维护解决方案的准确性低于50%......

近年来,预测性维护受到市场的广泛关注与重视,一度被预言是工业物联网的“杀手级”应用,吸引着众多企业涉足该领域,但它的应用却一直不及预期,被认为是当下最有需求、最有前途,也是最难落地的技术之一。
那么,预测性维护落地难的原因是什么?在实施前应做好哪些准备?如何有效推进预测性维护的落地?带着这些问题,e-works记者采访了三菱电机企划部软件应用科主管梁效。
01
与其说是技术问题
不如说是逻辑问题
当前,随着数字技术的快速发展,尤其是人工智能技术的突飞猛进,市场上已经涌现出众多预测性维护产品与解决方案提供商。然而,预测性维护落地比预想中困难。有数据统计,许多预测性维护解决方案的准确性低于50%。
“我认为落地难的原因,与其说是技术问题,不如说是逻辑问题。”梁效表示,推进预测性维护的核心前提是,紧密结合工业现场进行应用开发,而非简单地套用工具。虽然人工智能可以高效地进行模型训练,但只有结合工业现场的实际问题,深入掌握工业机理、工艺和设备等相关知识,才能真正确保预测性维护方案的有效性和实用性。例如,基于AI建模的前提是数据,企业只有收集到与故障课题在逻辑上紧密关联的数据,才能确保AI模型训练的精准度和有效性。因此,技术本身并不是最大的难题,真正的难点在于如何理解和分析复杂的工业过程,并准确地定义故障课题(实施对象);如何精准地建立故障课题与监测数据之间的逻辑关系,开展数据采集。
梁效坦言,当前大部分制造企业在这些方面明显不足,主要是缺乏对工业知识的系统归纳和积累。以加工工件为例,企业本应清楚识别生产工艺过程中故障产生的根源,如是扭矩、刀具硬度还是其他因素,但往往许多企业难以做到这一点。这种情况可能是工业现场人员的频繁流动、或是缺乏有效的知识沉淀与传承机制等所导致的。
梁效对于预测准确性的问题也提出了自己的见解。他指出,目前许多预测项目尚处于试错阶段,其准确性难以评估。同时,模型的性能表现受影响因素众多,如课题的总结、数据维度的列举、数据的清洗与筛选、算法的选择、模型的迭代与验证等。另外,企业对于项目成果的接受程度和容忍度也是衡量模型性能的一个重要因素。
预测准确性固然重要,但推进预测性维护的根本目标在于实现降本增效。因此,企业在预测性维护项目实施前,应进行全面的评估,包括分析设备故障频率、故障导致的停机时间、实施维护所需的时长,以及故障对生产活动的影响和造成的经济损失。在此基础上,计算通过实施预测性维护降低故障率所能带来的实际收益,进而判断该课题否值得投入。
02
基于原因分析
确定数据采集范围
推进预测性维护,最基层的便是有效的数据收集,其质量、数量和多样性对于模型的性能和可靠性至关重要。然而,很多预测性维护系统开发就卡壳在数据收集上。梁效表示,当前很多企业的数据采集基础较差,尤其是传统行业,或尚未建立完善的数采系统,或缺乏有效的数据积累。
预测性维护模型的建立与训练至少需要积累两类历史数据,一是故障数据,即计划外停机的数据;二是,设备运行状态数据,如电流、电压、温度、振动等各种数据。并且这两类数据的量足够,训练出的模型才更为准确。那么,数据量多少足够?梁效指出,数据量的充足性难以直接量化,需要结合企业的预期目标、对模型精度的要求等来综合判定。通常情况下,数据的积累应以月或年度为周期。同时,他强调,小数据在一定程度上可以解决数据量的问题。
在工业领域,小数据更加关注于具体场景下的数据,比如单个设备、特定过程或者小范围的环境。其可以提供更为详细和具体的洞察,有助于发现局部的模式、趋势和异常。具体到预测性维护,小数据对于工业现场的故障识别、设备优化等方面具有重要的应用价值。梁效指出,可以基于原因分析,开展有针对性的小数据采集。即企业基于对设备基理的深入理解,对可能导致故障的各种原因进行一一列举,并找到与故障成因最相关的因素,进行数据采集,再基于强相关维度的数据进行模行训练。通过这种方式,数据采集的范围更精确,模型的准确度也更高。
03
“三步走”构建预测性维护系统
在梁效看来,在确定课题后,预测性维护系统构建主要包括数据收集、离线分析、实时诊断三个关键步骤。即通过对业务流程、工艺知识等的有效梳理,对故障课题进行要因分析,确定收集什么数据及如何进行收集,如选择何种传感器,在哪些关键位置进行部署等。在此基础上,对数据进行预处理,分析数据并寻找数据间的潜在关联,提取与甄选关键特征,并通过AI算法开展线下模型训练与迭代,创建诊断模型,对其有效性进行验证。之后将模型部署到工业现场,通过诊断模型对未知数据进行实时诊断,快速识别出设备异常,在故障发生前(超过诊断模型中的定义阈值时)发出预警。
而为了帮助企业更高效的推进预测性维护项目,三菱电机打造了数据分析诊断软件MELSOFT MaiLab,涵盖数据集创建、AI模型的创建、任务的创建、任务的执行和监视四个核心功能(如下图)。该软件的诊断功能客户端可部署于IPC上位机,能够与各种诊断对象如PLC、加工机器和机器人进行连接和通信,也可以与SQL、MYSQL等传统数据库进行对接。
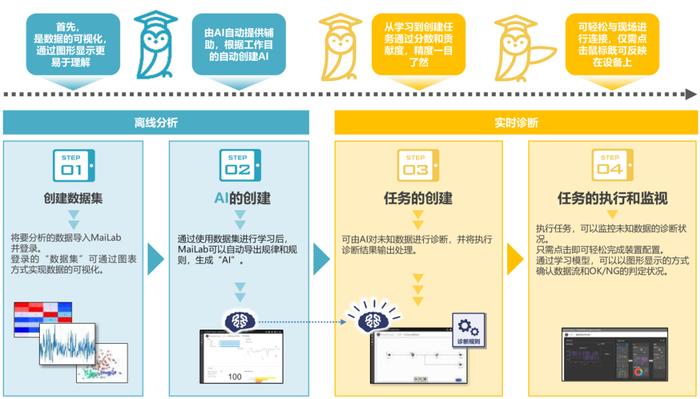
(来源:三菱电机)
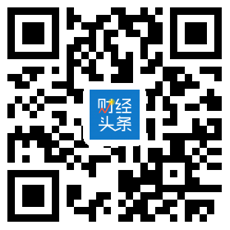
4000520066 欢迎批评指正
All Rights Reserved 新浪公司 版权所有