引言
在制造业的激烈竞争下,设备的高效运转是企业降本增效的核心。TPM(全面生产维护)管理中的“自主保全”机制,正是将设备维护责任从专业维修人员“下沉”到一线操作工的关键策略。然而,许多企业在推行自主保全时面临共性难题:操作工发现了设备异常,却不知如何高效处理。问题堆积可能导致小隐患演变为大故障,甚至引发停机损失。如何构建一套科学的问题处理闭环?本文从实践角度拆解关键步骤。
正文:四步构建自主保全问题处理闭环
一、快速响应:从“发现异常”到“分级上报”
自主保全的核心在于“早发现、早处理”。操作工在日常点检中若发现设备异响、漏油、温度异常等问题,需第一时间通过标准化流程上报。例如,某汽车制造企业采用“精益通APP”平台,操作工拍摄异常部位并标注问题,系统自动推送至维修班组,30分钟内响应。
关键动作:
明确上报标准:制定《设备异常识别清单》,细化常见问题(如螺栓松动、润滑不足)的判断标准,避免漏报或误报。
数字化工具赋能:通过移动端扫码报修、拍照上传等功能,实现问题可视化描述,缩短沟通成本。
二、精准施策:建立分类处理机制
并非所有问题都需停机维修。根据严重程度分级处理能显著提升效率:
1. 现场即时处理(占比60%):如清洁油污、紧固螺丝等基础保养,由操作工在班前10分钟内完成。某钣金车间通过培训,使操作工掌握17种常见小故障的修复技能,故障响应时间缩短70%。
2. 计划性维修(占比30%):对需停机处理的隐患(如传动部件磨损),纳入维修计划,利用生产间隙集中处理。
3. 技术攻关(占比10%):针对重复性故障或设计缺陷,组建跨部门小组进行根源分析。例如某电子厂针对贴片机频繁卡料问题,通过“5WHY分析法”锁定导轨材质缺陷,改造后故障率下降90%。
三、预防升级:从“救火”到“防火”
处理单一问题仅是治标,TPM更强调通过数据沉淀预防复发:
建立设备健康档案:记录每次异常现象、处理措施及后续跟踪数据,利用仪表盘分析高频故障点。某化工企业通过分析3年数据,发现离心泵密封圈平均每2000小时失效,据此优化备件更换周期,年节省维修成本120万元。
反向优化点检标准:将高频问题纳入点检表。如某食品厂在发现灌装机传感器易受潮后,在点检表中增加“每日检查传感器密封性”项,故障率下降65%。
四、文化筑基:让“人人都是设备管家”
长效机制的建立离不开组织文化的支撑:
技能可视化:通过“星级设备能手”认证体系,将处理问题的能力与职级晋升挂钩。某装备制造企业设置“初级-专家-大师”三级认证,大师级员工可参与设备选型决策。
即时激励:设置“金点子奖”“零故障班组”等荣誉,用仪式感强化参与意愿。某造纸企业每月公示“最佳问题处理案例”,获奖者可获得带薪培训机会,员工提案量提升3倍。
结论
TPM自主保全的本质,是通过“全员参与+流程闭环”将设备管理从被动维修转向主动防控。当一线员工既能精准识别异常,又能依托体系高效解决问题时,企业收获的不仅是设备利用率的提升,更培育出一支具备“工匠思维”的复合型团队。数据显示,成功实施该模式的企业,设备综合效率(OEE)平均提升15%-25%,这正是TPM“人机共赢”哲学的最佳诠释。
财经自媒体联盟
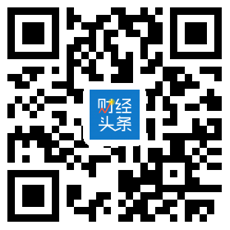
4000520066 欢迎批评指正
All Rights Reserved 新浪公司 版权所有