传统生产模式下,接链环的良品率低、工艺稳定性差等问题长期困扰行业。随着智能制造的深入应用,这一领域正迎来颠覆性变革——从“人工经验”到“数据驱动”,生产效率与产品质量实现双突破。本文将解析智能制造技术的核心应用场景,并探讨其如何重塑接链环行业。
技术突破一:全流程自动化生产线
痛点破解:人工误差与效率瓶颈
传统接链环生产依赖人工操作模具冲压、热处理等环节,易出现尺寸偏差、硬度不均等问题。山东某头部接链环制造商引入全自动冲压-热处理-检测一体化产线后,实现三大升级:
1.精准控温:通过物联网传感器实时监控热处理炉温,波动范围从±15℃缩减至±3℃,确保材料性能一致性;
2.视觉质检:自动识别表面裂纹、齿形偏差等缺陷,检测效率提升4倍,漏检率低于0.1%;
3.柔性生产:同一产线可快速切换生产立环、弧齿环等不同型号,订单响应周期缩短60%。
行业影响:以山东都尔伯特(DBT)为例,通过类似技术升级,接链环良品率提升至99.5%,生产成本下降18%。
技术突破二:数字孪生优化工艺参数
从“试错”到“预测”的跨越
过去,接链环的工艺参数调整依赖工程师经验,需反复试制样品验证。如今,数字孪生技术通过以下路径实现突破:
1.虚拟仿真:建立材料应力分布、磨损寿命等数字模型,提前预判设计缺陷;
2.参数优化:基于大数据分析,自动匹配最佳冲压速度、淬火时长等参数组合;
3.故障预警:实时监测设备状态,提前48小时预警模具磨损风险,减少停机损失。
技术突破三:区块链溯源提升供应链透明度
破解“质量信任”难题
针对客户对原材料来源的质疑,部分企业引入区块链技术:
1.材料溯源:从钢材采购到成品出厂,全流程数据上链,客户可随时查验供应商资质、检测报告;
2.智能合约:自动触发质检流程,不合格批次直接拦截,避免流入市场;
3.数据共享:下游企业可基于链上数据优化设备维护计划,降低突发故障风险。
行业观察:技术红利催生新格局
在智能制造浪潮下,接链环行业呈现两大趋势:
1.头部企业技术壁垒增强:通过“5G+工业互联网”实现远程运维,客户可通过手机端实时查看生产进度,订单交付准时率达98%;
2.中小企业加速转型:云平台提供的低成本MES(制造执行系统)解决方案,帮助中小厂商快速接入智能化改造,行业集中度逐步提升。
未来属于“数据驱动的制造者”
智能制造不仅改变了接链环的生产方式,更重新定义了质量与效率的平衡点。从自动化产线到数字孪生,从区块链溯源到工业互联网,每一项技术都在推动行业向更高可靠性、更低成本的方向进化。
以山东都尔伯特(DBT)为例,其部分技术升级成果已在实际场景中得到验证:在某矿山项目中,其生产的矿用接链环凭借智能化工艺和严格品控,实现连续12个月无故障运行,客户主动将采购份额提升30%。这种以数据为驱动的制造模式,不仅为企业赢得了客户信赖,也为国产接链环的全球化竞争提供了新范本。
对于行业而言,抓住智能制造的红利,或许就是赢得未来市场竞争的关键钥匙。
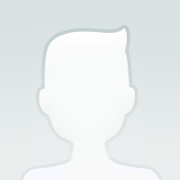
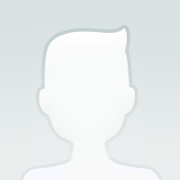
财经自媒体联盟
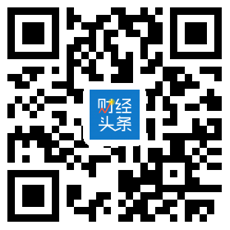
4000520066 欢迎批评指正
All Rights Reserved 新浪公司 版权所有