无尘车间作为现代精密制造业的核心基础设施,其应用范围已从传统的半导体、医药领域扩展到新能源、生物科技等新兴行业。这种高度受控的环境通过空气过滤系统、温湿度调节和严格的污染物管控,为高精度生产提供了必要条件,但其建设和运营过程中也面临技术、成本和管理等多重挑战。合洁科技电子净化工程公司将从技术原理、行业应用、实施难点及未来趋势等维度展开分析。
一、技术优势与核心价值
1、微粒控制技术
采用HEPA/ULPA过滤系统可过滤99.97%-99.9995%的0.3μm以上颗粒,在半导体晶圆制造中,每立方米空气中≥0.5μm的颗粒需控制在10个以内。某芯片代工厂的数据显示,洁净度提升至ISO3级后,晶圆良品率提高了18%。
2、环境参数精确调控
温度波动需控制在±0.5℃范围内,湿度偏差不超过±5%。某液晶面板厂的案例表明,将湿度稳定在45%±3%后,显示面板的静电损伤率下降40%。
3、交叉污染防护体系
通过气压梯度设计(如医药车间保持5-15Pa正压差)和物料净化流程,某疫苗生产企业将批次间污染事件从年均5次降至零。
二、行业应用差异分析
半导体行业:要求ISO1-3级洁净度,建设成本达每平方米2-3万元,但可降低纳米级线路的短路风险。某12英寸晶圆厂通过升级FFU系统,使设备停机时间减少23%。
医药无菌制剂:需符合GMP A级标准,人员更衣程序耗时30分钟以上,但能确保注射剂无菌合格率≥99.99%。
锂电隔膜生产:虽然仅需ISO 7-8级,但需额外控制金属离子浓度至ppb级,某头部厂商通过引入离子过滤装置使产品不良率降低15%。
三、实施中的关键挑战
1、能耗矛盾
洁净室能耗是普通空调厂房的10-15倍,某光伏企业采用变频风机+热回收系统后,年节电达280万度。但初始改造成本需18个月才能收回。
2、动态污染控制
人员活动会使微粒浓度瞬时增加5-8倍,某微电子工厂通过智能门禁系统限制区域人数,使洁净度波动幅度降低62%。
3、维护成本高企
过滤器年更换成本约占运维费用的35%,某生物实验室采用预过滤+寿命预测系统,将高效过滤器使用周期延长至5年。
4、标准适配难题
医疗器械行业同时满足GMP与ISO 14644标准时,需增加30%的验证工作量。某IVD企业通过建立统一管控平台,使合规审查时间缩短40%。
四、技术创新方向
1、智能化监控系统
某面板厂部署的IoT传感器网络,可实现微粒浓度的实时三维定位,异常响应时间从45分钟缩短至8分钟。
2、绿色节能方案
磁悬浮风机+干盘管技术的应用案例显示,可降低空调系统能耗42%。光伏洁净车间屋顶的实践表明,可再生能源可满足15-20%的电力需求。
3、模块化建设模式
预制式洁净室的安装周期比传统方式缩短60%,某基因测序中心采用可扩展模块设计,使产能提升时的改造成本降低55%。
五、管理优化实践
人员培训体系:某药厂实施的VR模拟训练,使新员工操作失误率下降70%
物料管理创新:AGV+气闸通道的组合方案,使物料传输污染风险降低90%
应急响应机制:基于FMEA分析的应急预案,可将污染事件处理效率提升50%
当前,随着纳米技术和基因编辑等前沿领域的发展,对洁净环境的要求正从微粒控制向分子级污染防控延伸。未来五年,自清洁材料、量子传感等技术的突破,或将使无尘车间的运营成本降低30-40%。但行业也需警惕过度洁净导致的"免疫缺陷"问题——某研究所数据显示,长期在ISO 4级以上环境工作的人员,呼吸道疾病发病率是普通环境的1.8倍。如何在技术精益与可持续发展之间取得平衡,将成为下一代洁净技术研发的核心命题。
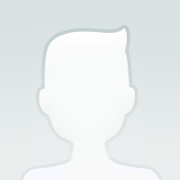
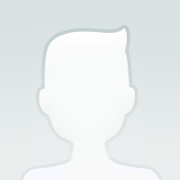
财经自媒体联盟
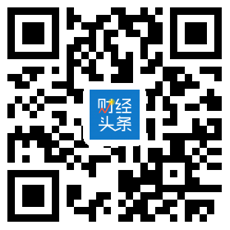
4000520066 欢迎批评指正
All Rights Reserved 新浪公司 版权所有